Le batteur de Panic ! At the Disco mise sur l’impression 3D pour réinventer les percussions
- Shiva Cloud Security Fr
- 21 déc. 2019
- 4 min de lecture
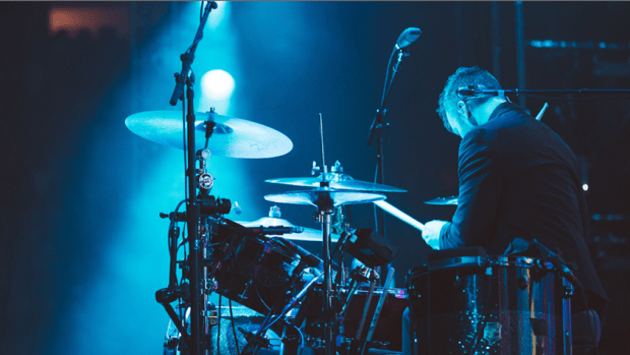
Dan Pawlovich, batteur du groupe Panic! At The Disco, explique comment l’impression 3D et le prototypage permettent aux bricoleurs d’essayer de nouvelles idées et de changer l’industrie.
Pawlovich utilise Stratasys Direct pour imprimer les caisses claires qu’il utilise en tournée. Pawlovich s’intéresse à la conception de batterie depuis son adolescence, dans son groupe de garage de l’époque, il a repeint un kit de batterie pour le personnaliser. ZDNet a rencontré Pawlovich pour parler de l’impression 3D.
“Le design de batterie est quelque chose qui me préoccupe depuis d’innombrables années. Ce que je voulais dans ma tête était une caisse de tambour en bois avec des cornes sur la coque”, a-t-il expliqué. “Le problème était qu’il n’y avait pas de moyen viable de le faire.”
Et puis nous avons regardé une vidéo en ligne d’une personne imprimant en 3D une clé à molette fonctionnelle. “Heureusement, je n’étais pas bloqué sur le bois”, a déclaré Pawlovich. “S’il y a un problème qui semble impossible, cela ne m’importe pas beaucoup parce que je crois toujours qu’il sera résolu un jour. Je vais juste travailler sur autre chose et y revenir plus tard.”
Avant d’arriver au point où Pawlovich pouvait réellement utiliser des pièces qu’il a conçues, il a fallu environ 6 à 7 ans. La moitié de ce temps a été consacrée à la conception assistée par ordinateur d’un design, puis à la phase de prototypage, chaque millimètre et chaque mesure compte. La première impression via Stratasys remonte à environ 3 ans. “Il n’y a pas de place pour les erreurs au-delà de 1 mm”, explique-t-il.
Voici un aperçu de l’approche et du processus de réflexion de Pawlovich avec la conception de ses propres fûts.
publicité
Le plaisir, l’art, la science
Pawlovich s’est lancé dans la conception de fûts en grande partie parce que c’était amusant. “Jusqu’à présent, tout était amusant. Concevoir ce fût et mettre un peu d’argent pour les changements de design était amusant. Obtenir des impressions correctes était presque très amusant”, a-t-il déclaré.
L’objectif était de produire des tambours qui sonnaient aussi bien que les normaux, puis de jeter les bases pour des fûts capables de produire des sons personnalisés et une approche musicale unique. En tournée, Pawlovich avait besoin d’un fût imprimé en 3D capable de gérer les fluctuations de température, la lumière UV tout en fonctionnant avec des pièces standard de l’industrie.
“Une fois que cela ressemblait à ce que je voulais, nous devions espérer que cela sonnerait bien”, a-t-il déclaré. En tournée, Pawlovich a essayé son fût imprimé en 3D dans les coulisses de la Green Room et il a compris qu’il tenait quelque chose.
Pourquoi changer les designs?
Un fût traditionnel a une coque en bois ou en métal avec des jantes et des attaches en métal qui fixent la tête de fût sur la coque. Un fût a une note claire lorsqu’il est tapé doucement, mais la précision de la hauteur fondamentale est perdue avec des pièces métalliques fixées à la coque.
Pawlovich cherchait quelque chose qui sonnait mieux. En incorporant des cosses métalliques directement dans la coque du tambour, l’addition de nouveaux éléments ne peut pas nuire à la clarté musicale.
La technologie d’impression 3D utilisée est similaire au frittage laser ou laser sintering. Cette technique construit une pièce à partir de données CAO 3D via un laser CO2 qui fusionne les thermoplastiques couche par couche.
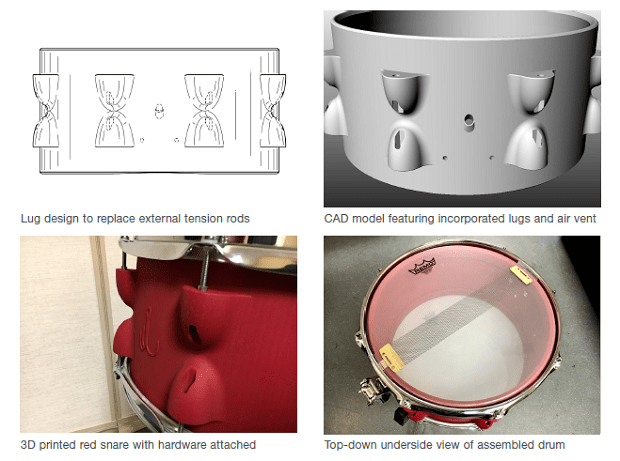
Pawlovich a dû bricoler le design pour pouvoir utiliser des tiges de tension, des jantes et des têtes de tambour traditionnelles. Après plusieurs faux départs, Stratasys Direct a imprimé un prototype en utilisant du matériau Nylon 12GF et un processus de teinture appelé ColorTek pour produire une coque de tambour rouge. En prime, le nylon 12GF peut gérer les fluctuations de température, l’humidité et la lumière UV.
Pawlovich a enregistré des expériences pour comparer des caisses claires imprimées en 3D avec une version traditionnelle. Celle imprimée en 3D était aussi bonne sinon meilleure.
Un business en vue ?
Pawlovich possède des brevets sur la conception et l’utilité de ses fûts imprimés en 3D : le dépôt de ceux-ci a pris environ aussi longtemps que le processus de conception total. “J’étais complètement novice dans le processus de brevet. Il est plus intense encore que le processus de conception”, a-t-il déclaré. Someday Pawlovich a peut-être sa propre ligne de batterie, mais pour l’instant le côté commercial lui paraît difficile à imaginer. “Chaque fois que je pense à l’aspect commercial, je sens un poids sur mes épaules”, a déclaré Pawlovich.
“J’adore la vie que je vis en tant que musicien en ce moment.” Pawlovich a également déclaré qu’il se rend compte que l’aspect commercial prend du temps. Lors de la préparation d’une tournée, il faut 6 à 8 mois pour caler les détails. Vous ne pouvez pas vraiment démarrer une entreprise en tournée. “J’espère voir d’autres fabricants de batteries embrasser l’idée et m’apprendre montrer une chose ou deux ou 1 000. Pour l’instant, nous n’avons construit qu’un seul fût qui montre qu’il peut fonctionner avec des pièces traditionnelles”, a déclaré Pawlovich.
En attendant, Pawlovich va bricoler. “Nous avons apporté quelques modifications de conception et avons lentement constitué nos fichiers et nos options pour repousser les limites”, a-t-il déclaré. Pawlovich a déjà conçu une deuxième itération avec une caisse claire de 5 pouces et demi de profondeur. La taille réduite a nécessité une refonte des pattes et du diamètre de la coque.
Source : ZDNet.com
Comments